[High frequency welder]Introduction to High Frequency Welder: A Comprehensive Guide
News 2025-6-29
In the realm of welding technology, high frequency welders have become increasingly significant due to their ability to perform precise and efficient welding operations. This article will provide a comprehensive introduction to high frequency welders, discussing their applications, advantages, and operational principles.
What is a High Frequency Welder?
High frequency welders are advanced welding machines that utilize high-frequency electrical currents to generate heat for joining materials. They are typically used in the manufacturing industry for sealing plastic parts, joining thin metal sheets, or creating hermetic seals in medical devices. High frequency welding offers a non-contact method of welding, which means the welding process can be carried out without direct contact between the welding tool and the material being welded.
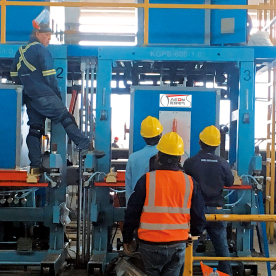
Introduction to High Frequency Welder: A Comprehensive Guide
High frequency welders have numerous applications across various industries. They are commonly used in the automotive, medical, packaging, and electronics industries. Some of the specific applications include:
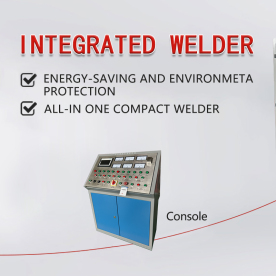
Introduction to High Frequency Welder: A Comprehensive Guide
Advantages of High Frequency Welders
High frequency welders offer several advantages over traditional welding methods:
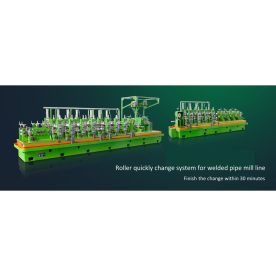
Introduction to High Frequency Welder: A Comprehensive Guide
Operational Principles of High Frequency Welders
High frequency welders generate high-frequency electrical currents that are transmitted through electrodes or a contact plate to the materials being welded. The high-frequency current induces resistance heating in the materials, causing them to melt and fuse together. The welding process is controlled by adjusting parameters such as current amplitude, frequency, and welding time to achieve the desired weld quality.
In summary, high frequency welders are essential for various manufacturing processes that require precise and efficient welding operations. They offer numerous advantages over traditional welding methods and are widely used in various industries such as automotive, medical, packaging, and electronics. As technology continues to evolve, high frequency welders are becoming more advanced and are capable of handling more complex welding applications.