[Mould for tube mill]Innovative Approaches to Utilizing Mould for Tube Mill Production: Enhancing Quality and Efficiency in Manufacturing Processes
News 2024-12-31
Introduction
In the world of metalworking and manufacturing, the production of tubes has gained immense importance due to the increasing demand for versatile applications in industries such as automotive, aerospace, construction, and energy. At the heart of tube manufacturing is the tube mill, a sophisticated piece of machinery that shapes flat metal strips into tubular forms. One of the critical components that significantly influences the performance and quality of the tube mill is the mould. In this article, we will explore the pivotal role of mould in tube mill processes, the advancements in mould technology, and how these developments are transforming the production of tubes for various applications.
The Role of Mould in Tube Mills
Moulds are essential components in tube mills, as they define the final shape and dimensions of the tubes being produced. A mould's primary function is to guide the metal strip through various stages of shaping, ensuring that the final product meets specific dimensional and structural requirements. The process involves feeding the flat strip into the tube mill, where it undergoes a series of forming processes, including welding and shaping, facilitated by the mould.
The efficiency of the mould directly impacts the overall productivity of the tube mill. A well-designed mould leads to precision forming, reduces wastage, and minimizes defects in the produced tubes. As industries diversify and demand for customized tube specifications increases, advancements in mould technology have become more crucial than ever in meeting these challenges.
Advancements in Mould Technology
Mould technology for tube mills has evolved significantly, with innovations that enhance both performance and longevity. Here are some key advancements:
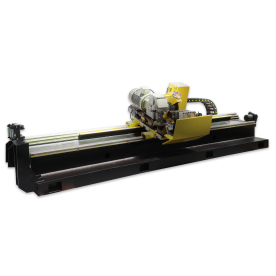
Innovative Approaches to Utilizing Mould for Tube Mill Production: Enhancing Quality and Efficiency in Manufacturing Processes
2. **Modular Design**: Manufacturing processes are realizing the advantages of modular mould designs, which allow for quick changes in mould configurations. This flexibility caters to varying production requirements and enables manufacturers to switch between different tube sizes with ease, thereby minimizing downtime and maximizing production efficiency.
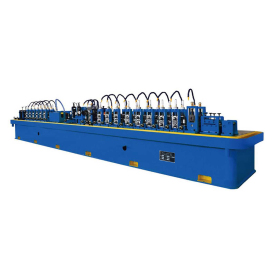
Innovative Approaches to Utilizing Mould for Tube Mill Production: Enhancing Quality and Efficiency in Manufacturing Processes
4. **Additive Manufacturing**: The advent of 3D printing and additive manufacturing has opened new avenues for mould development. These technologies allow for rapid prototyping of mould designs, enabling manufacturers to test and refine mould configurations quickly. This innovation can lead to more economical and efficient production processes, as complex designs can be realized that would be difficult to produce with traditional methods.
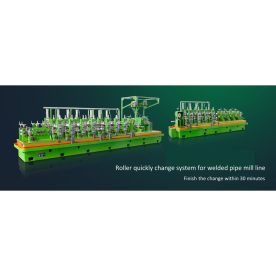
Innovative Approaches to Utilizing Mould for Tube Mill Production: Enhancing Quality and Efficiency in Manufacturing Processes
Enhancing Quality and Efficiency
The innovations in mould technology not only improve the efficiency of tube mills but also enhance the quality of the tubes produced. With higher precision, manufacturers can ensure that tubes meet stringent industry standards for strength, flexibility, and durability. This quality assurance is particularly vital in applications where the structural integrity of the tubes is critical, such as in oil and gas pipelines or construction materials.
Moreover, the reduction of waste through more efficient mould designs contributes to sustainable manufacturing practices. Manufacturers are increasingly focused on minimizing their environmental footprint, and optimized mould production plays a significant role in achieving this goal.
Conclusion
In conclusion, the mould is a critical component in tube milling processes that greatly influences both productivity and quality. As industries continue to evolve with diverse applications for tubular products, the need for advanced mould technology becomes increasingly important. Embracing innovations such as improved materials, modular designs, CNC machining, additive manufacturing, and integrated sensors will not only enhance tube mill efficiency but also ensure that the highest standards of quality are met. As we look forward to the future of manufacturing, the role of mould in tube mills will undoubtedly become even more crucial in shaping the metalworking industry's landscape.