[Pipe mill production line with quality control measures]Ensuring Precision and Excellence: The Role of Quality Control Measures in Pipe Mill Production Line Operations
News 2024-12-1
****In the world of manufacturing, particularly in the pipe production industry, maintaining high standards of quality is not merely a matter of compliance; it is essential for ensuring the longevity and reliability of the products. The pipe mill production line, where raw materials are transformed into finished products, plays a crucial role in various applications, from construction to oil and gas. Within this context, quality control measures are vital to ensuring that every pipe produced meets the stringent requirements of safety, durability, and performance. This article explores the intricacies of pipe mill production lines and underscores the importance of implementing effective quality control procedures throughout the process.
Overview of Pipe Mill Production Line
The pipe mill production line consists of several stages, from raw material processing to the final inspection of finished pipes. The primary raw material used in pipe manufacturing is steel, which is subjected to various processes, including welding, cutting, and bending, to create the desired pipe configuration. The production line is typically composed of the following stages:
1. **Raw Material Preparation**: This initial stage involves quality checks on incoming raw materials, ensuring they meet industry standards and specifications.
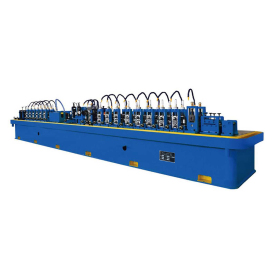
Ensuring Precision and Excellence: The Role of Quality Control Measures in Pipe Mill Production Line Operations
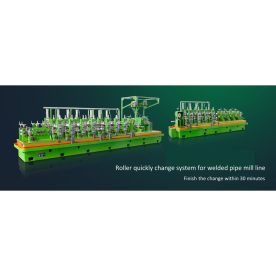
Ensuring Precision and Excellence: The Role of Quality Control Measures in Pipe Mill Production Line Operations
4. **Heat Treatment**: Certain types of pipes undergo heat treatments to enhance their mechanical properties. This step is crucial for applications in harsh environments, as it can significantly impact the pipe’s performance under stress.
5. **Finishing Operations**: This includes processes such as coating and cleaning, which not only prepare the pipes for shipment but also improve their corrosion resistance and aesthetic appearance.
6. **Quality Control Inspection**: The final stage involves thorough inspections and tests to confirm that the pipes meet all specified standards.
The Importance of Quality Control Measures
Quality control measures in the pipe mill production line serve several critical functions. First and foremost, they help ensure product compliance with industry standards and regulations, which are essential for customer trust and product reliability. Any defects in structure or material could result in safety risks, especially in high-stakes industries like oil and gas, where pipeline failures could have catastrophic effects.
Moreover, implementing quality control measures can lead to cost savings in the long run. By identifying and addressing issues early in the production process, manufacturers can minimize waste, reduce rework, and diminish the risk of product returns or liability claims. This proactive approach not only enhances operational efficiency but also promotes a culture of continuous improvement among employees.
Key Quality Control Measures
Several specific quality control measures can be implemented throughout the pipe mill production line to enhance product quality:
1. **Material Inspection**: Utilizing non-destructive testing methods such as ultrasonic testing or X-ray inspection allows manufacturers to verify the integrity of raw materials and welds without compromising their structure.
2. **Process Monitoring**: Continuous monitoring of production parameters, such as temperature, pressure, and feeding speeds, can help identify deviations from set standards in real time, enabling quick corrective actions.
3. **Statistical Process Control (SPC)**: Employing statistical analysis tools allows manufacturers to evaluate variability in the production process and make data-driven decisions to minimize defects.
4. **Final Product Testing**: Rigorous testing of finished products, including pressure testing, hardness testing, and dimensional checks, ensures that every pipe can perform as required under various operational conditions.
5. **Employee Training**: Regular training sessions for staff on quality standards and control measures can cultivate a workforce that is more vigilant and proactive about quality assurance.
Conclusion
