[High frequency welder]Understanding High Frequency Welders: Their Mechanism, Applications, and Advantages in Modern Manufacturing Processes
News 2024-11-29
In today’s fast-paced manufacturing environment, efficiency and precision are paramount. Among the numerous technologies that facilitate these requirements, high frequency welding has emerged as a highly effective method for joining materials, particularly in metalworking and plastics. High frequency welders utilize advanced techniques that allow for fast and reliable bonding, making them invaluable tools in various industrial applications. This article delves into the workings of high frequency welders, their uses across different sectors, and the numerous advantages they offer.
What is High Frequency Welding?
High frequency welding, also known as radio frequency (RF) welding, is a process that employs electromagnetic waves to generate heat within a material, allowing for the joining of two or more pieces. The technology is particularly effective for thermoplastic materials, as the high frequencies can induce molecular agitation that leads to softening and eventually melting of the material at the weld interface. As the layers of the materials reach their melting point, they are pressed together, forming a strong bond once cooled.
The frequency used during this process typically falls within the range of 13.56 MHz to 40.68 MHz. The equipment involved in high frequency welding includes a high frequency welder, which consists of a generator and a welding head. The generator produces the required electromagnetic waves, while the welding head concentrates these waves at the welding site.
How Does High Frequency Welding Work?
The high frequency welding process involves several critical steps. Initially, the materials that need to be joined are prepared and aligned in the welder. Next, the welder's electromagnetic field is activated, targeting the specific areas where the materials will be fused. The induced heat causes the molecular structure of the thermoplastic materials to soften, allowing them to flow together under pressure. After a brief period, the pressure is maintained while the material cools down and solidifies, creating a robust and durable bond.
The speed of this entire process is one of its most significant advantages; high frequency welding can often produce quality welds in mere seconds. This rapid joining capability enhances productivity on manufacturing lines, enabling companies to meet high demand swiftly.
Applications of High Frequency Welders
High frequency welders have found applications across various industries, primarily those involving plastics or thin metals. Below are some of the critical sectors where this technology is heavily utilized:
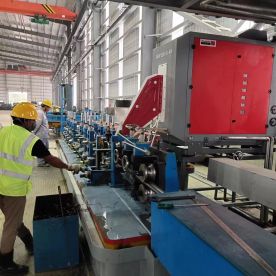
Understanding High Frequency Welders: Their Mechanism, Applications, and Advantages in Modern Manufacturing Processes
2. **Automotive Manufacturing**: In the automotive sector, high frequency welders are used for assembling interior components, securing insulation layers, and even fusing certain electronic parts.
3. **Medical Device Production**: The medical industry employs high frequency welding for packaging medical devices, manufacturing sterile packaging, and constructing wearable devices. The technology ensures a clean and strong seal that is critical for maintaining product integrity and safety.
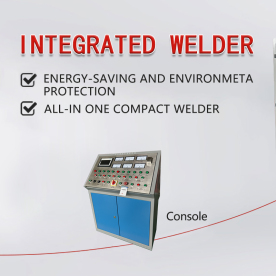
Understanding High Frequency Welders: Their Mechanism, Applications, and Advantages in Modern Manufacturing Processes
Advantages of Using High Frequency Welders
Engaging high frequency welders offers numerous benefits, including:
- **Speed and Efficiency**: As mentioned earlier, high frequency welding can significantly reduce production times, which in turn can lead to increased throughput and lower labor costs.
- **Strength of Welds**: The bonds created using this method are often stronger than traditional adhesive methods, resulting in durable products that stand the test of time.
- **Versatility**: High frequency welding can be applied to a vast array of materials, including various types of plastics and thin metals, making it suitable for diverse manufacturing needs.
- **Eco-friendliness**: This type of welding does not typically require adhesives or solvents, resulting in less waste and a lower environmental impact.
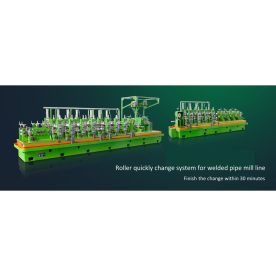