[Pipe mill production line with welding and cutting functions]Exploring the Innovative Pipe Mill Production Line: Integrating Advanced Welding and Cutting Functions for Enhanced Efficiency and Quality
News 2024-11-29
In the fast-paced world of manufacturing, efficiency and precision are paramount. This is especially true in the production of pipes, where the seamless integration of advanced technologies can make a significant difference in overall output and quality. A key innovation in this arena is the pipe mill production line, which incorporates sophisticated welding and cutting functions. This article delves into the features, benefits, and advantages of such a production line, shedding light on how it transforms traditional manufacturing processes.
At the heart of a pipe mill production line lies its ability to produce seamless and welded pipes efficiently. The line typically comprises several key components: a forming section, welding unit, and cutting station. Each element plays a critical role in ensuring that the finished product meets exacting industry standards, particularly in sectors like construction, oil and gas, and automotive manufacturing.
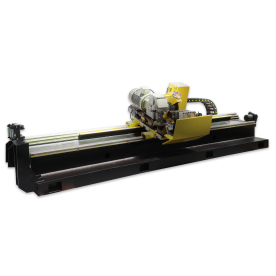
Exploring the Innovative Pipe Mill Production Line: Integrating Advanced Welding and Cutting Functions for Enhanced Efficiency and Quality
In addition, the integration of cutting functions into the pipe mill production line greatly enhances flexibility and efficiency. Once the pipes are formed and welded, the cutting unit is responsible for precisely cutting them to the desired lengths. Advanced cutting technologies, such as laser cutting and plasma cutting, offer exceptional accuracy and reduced material wastage. Laser cutting, for instance, employs a focused beam of light to achieve clean cuts, which minimizes the need for secondary processing.
Another critical aspect of modern pipe mill production lines is the automation of various processes. Automated systems reduce the potential for human error and increase production speed, allowing manufacturers to meet higher demand with consistent quality. Smart sensors and controls can monitor each stage of production, adjusting parameters in real-time to maintain optimum conditions for welding and cutting. Consequently, this automation not only boosts productivity but also enhances the safety of the operation by minimizing manual handling of heavy materials.
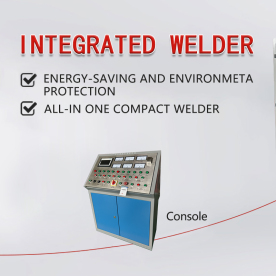
Exploring the Innovative Pipe Mill Production Line: Integrating Advanced Welding and Cutting Functions for Enhanced Efficiency and Quality
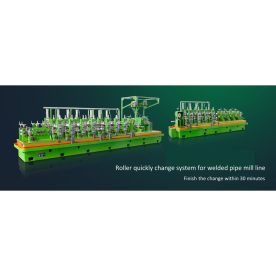
Exploring the Innovative Pipe Mill Production Line: Integrating Advanced Welding and Cutting Functions for Enhanced Efficiency and Quality
The environmental impact of pipe mill production lines equipped with advanced welding and cutting functions is also worth mentioning. By utilizing technologies that require less energy and produce fewer emissions, manufacturers can align their operations with sustainability goals. For instance, less material waste generated from precise cutting processes means reduced overall resource consumption, contributing to more environmentally friendly production practices.
In terms of quality control, modern pipe mill production lines often integrate inspection systems that can assess the integrity of welds and measure the dimensions of the finished pipes. Automated inspection technologies, such as non-destructive testing (NDT), ensure that any defects are caught early in the process, preventing costly rework and ensuring compliance with industry standards.
In conclusion, the integration of welding and cutting functions in pipe mill production lines represents a significant advancement in manufacturing technology. These modern systems not only enhance efficiency and flexibility but also improve product quality and sustainability. As industries continue to evolve and demand more from their suppliers, the innovations present in advanced pipe mill production lines will be essential in shaping the future of pipe manufacturing. By investing in such technologies, manufacturers can position themselves at the forefront of the industry, equipped to meet the challenges and opportunities that lie ahead.